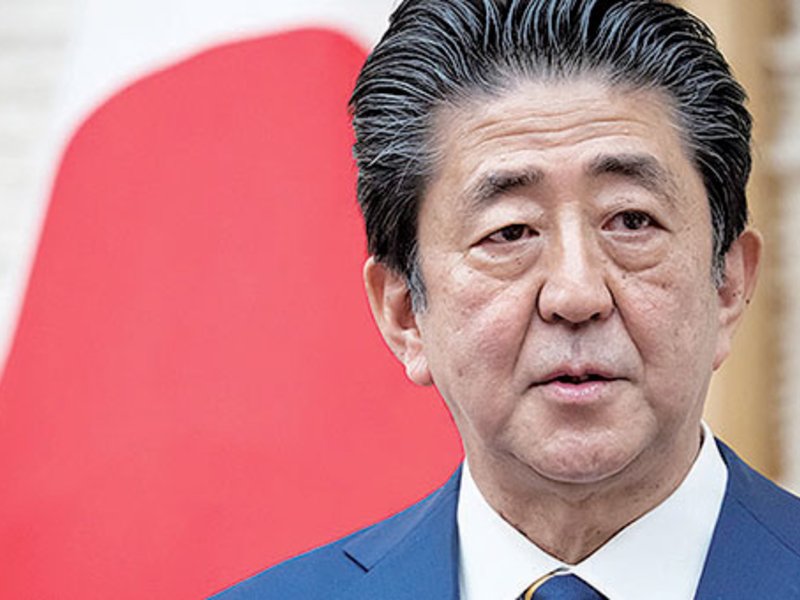
TOKYO — Toyota was quick to respond to the COVID-19 pandemic in the U.S. with plans to make medical face shields. Now that the Japanese government has declared a state of emergency in its home market, Toyota is rallying resources to fight the spread here.
Toyota’s plan for Japan — similar to what automakers are doing in the U.S. — includes making face masks, producing face shields, building hospital beds, fabricating emergency partition walls and churning out other medical supplies.
To do that, the company is marshaling the full force of the Toyota Group constellation of partner companies and suppliers. It draws on the manufacturing firepower of Aisin Seiki Co., Denso Corp. and Toyota Boshoku Corp.
Toyota outlined the strategy last week as Japan Prime Minister Shinzo Abe declared a state of emergency in major metropolitan areas as coronavirus infections rise. Some experts fear Japan is on the edge of a massive outbreak.
The government’s decree stops short of a full lockdown, but it enables local governors to close nonessential businesses in cities such as Tokyo, Yokohama, Osaka and Fukuoka.
Japan had 5,530 cases of coronavirus infection by late last week, according to international tracking site Worldometers, while 99 people have died.
Toyota said it will work to fight the pandemic and strengthen its business so the company can survive the economic downturn.
Automotive production throughout Japan has essentially ground to a halt as Toyota, Honda, Nissan, Mitsubishi, Mazda and Subaru all temporarily suspend lines in response to supply chain problems and efforts to pare inventories in the face of plunging global demand.
“Toyota will do what it can to help efforts on the front lines of treatment and in limiting the further spread of COVID-19, which has become society’s biggest priority,” the company said in a news release last week.
“While engaging in efforts to help suppress the spread of the virus and support the medical professionals on the front lines, the most urgent issues, Toyota also sees a need to be prepared for the recovery of economic activity following a return to normalcy.”
Toyota will produce 500 to 600 injection-molded and 3D-printed medical face shields a week at its Teiho machinery-making plant. It also will advise medical equipment makers on ways to increase output of ventilators and other items by using the efficiency concepts of the Toyota Production System.
The carmaker also will leverage its supplier group to make face masks. The idea is for the companies to make their own masks and alleviate demand on the open market. Denso aims to make 100,000 a day, while Toyota Boshoku chips in another 13,500 daily. Aisin Seiki, Toyota Motor, Daihatsu and Hino also are considering their own production.
Aisin Seiki — in addition to making powertrain, chassis and electrical components for automobiles — has a small household equipment unit that makes such things as toilet seats. It plans to make beds, disinfectant containers and partition walls for makeshift hospitals.
Toyota said it will double down on cost innovation during the pandemic to shore up profitability. The company pledged to “go back to its founding principles to eliminate ‘extra fat’ and shift to a leaner corporate structure by using the knowledge it gains this time to thoroughly review its capital investment, R&D expenses and required personnel.”