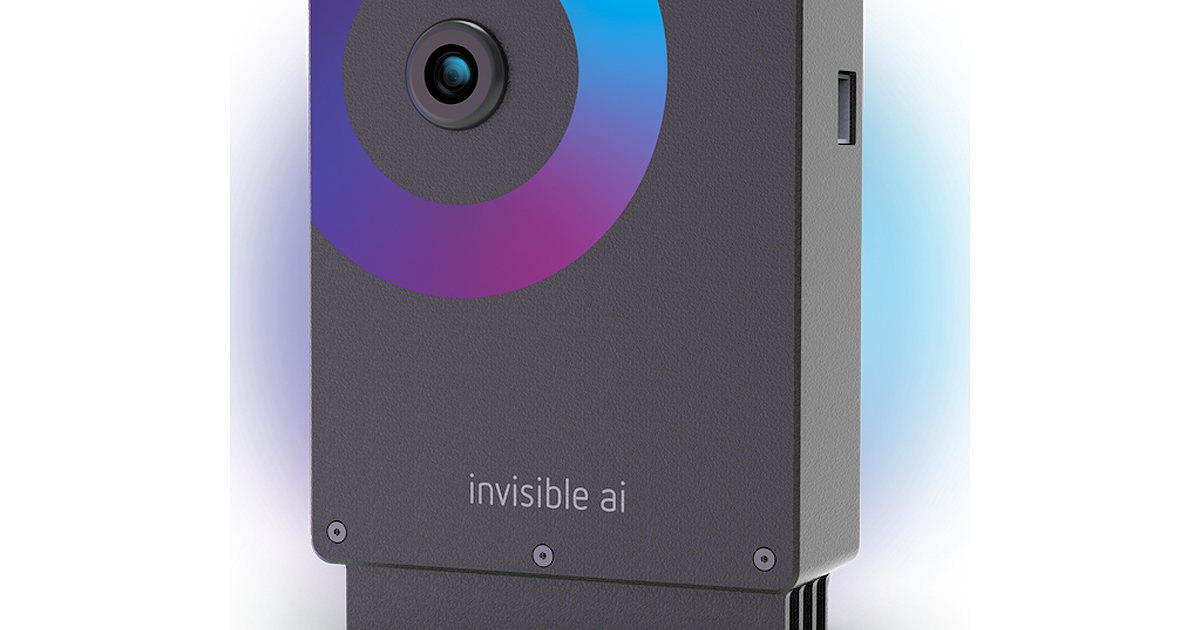
Toyota Motor Corp., whose production system is widely emulated around the auto industry, will soon begin installing technology in its plants that holds the promise of the holy grail of efficiency: automated kaizen.
Or at least almost automated.
The automaker has partnered with an Austin, Texas, startup to install thousands of units across its network of North American factories that will inconspicuously track workers’ joint and eye motions as they move through their daily assembly processes.
The tablet-sized units made up of a camera, processor and data storage in a single box will analyze those movements — without the need for supervisors watching or team members wearing tracking sensors — and then use artificial intelligence to suss out improvements in efficiency and safety. They will also notify the worker in real time when they’ve completed the task correctly.
The system, developed by Invisible AI — a startup with 17 full-time employees — will be deployed first at Toyota’s massive assembly plant in Princeton, Ind., and then spread across the automaker’s 14 other manufacturing plants in North America.
Toyota has been piloting the devices in smaller numbers at Princeton, but it is now moving to a much broader utilization of the technology.
Kaizen, or continuous improvement, efforts are at the core of the Toyota Production System. All over the world, Toyota team members and managers search for every small improvement they can identify to eliminate a wasteful motion or a process that might be detrimental to operations.
But Stephen Brennan, Toyota’s group vice president of vehicle production engineering and the Manufacturing Project Innovation Center, told Automotive News that, historically, identifying kaizens has been done through observation. The Invisible AI devices will now “help us increase the frequency and accuracy of process reviews as well as reduce the time needed to find inefficiencies across processes, giving us more time to focus on improvement.”
The Princeton plant, where the Toyota Highlander and Sienna are assembled, is undergoing an $803 million renovation to enable production of the new larger Toyota Grand Highlander and Lexus TX three-row crossovers beginning next year.
About 500 of the Invisible AI boxes initially will be installed in half of the plant, then installation will expand to the other half later, Eric Danziger, co-founder and CEO of Invisible AI, told Automotive News last week.
“All the methods [companies] use right now to measure productivity, to measure throughput, to find bottlenecks — those are things that someone comes on the line and just does five examples or maybe 20. But they’re not doing 6,000 because they don’t have the ability to do that level of time statistics,” Danziger explained. “They don’t have the ability to see across shifts, across operators, across all these different dimensions.”
But the Invisible AI devices can “give them weeks and weeks and weeks of data that they can analyze to find those bottlenecks and make sure that they’re making those productivity improvements,” he said.
Each device tracks one workstation and processes body motion data to identify the potential for high-stress injuries. It can detect movements that might be physically onerous to a worker on that job over time.
The devices can also detect simple defects in real time, explained Prateek Sachdeva, co-founder and COO of Invisible AI. It can “help prevent defects that are impossible to track without looking at the operators themselves.”
It can alert an operator, for example, that a connection was not fully made.
“We have focused on safety pillars by focusing on the ergonomics and measuring and helping [Toyota] to proactively look at issues. And that same applies to efficiency and productivity,” Sachdeva said.
The camera systems also promise to vastly reduce “root cause analysis” time during defect studies or safety audits, Sachdeva said, because the motion captures of each job are stored right there.
The key to the Invisible AI devices, Danziger explained, is that they are self-contained and capture, store and analyze their own information instead of taking up valuable bandwidth sending data to a centralized hub.
In his role, Brennan oversees the teams who lead Toyota’s product launches. He said the automaker is also studying the devices’ potential use in improving safety and ergonomics.
“Big data is crucial for process optimization and flexibility,” he said. “But with data sets so large and complex, it becomes difficult to process using traditional data processing applications.
Invisible AI “is relatively easy to use by production team leaders and group leaders, and the data analysis is done on-site, minimizing the need for large network infrastructures,” he said.
“We’re looking to use Invisible AI to bridge that gap for the human component of manufacturing.”