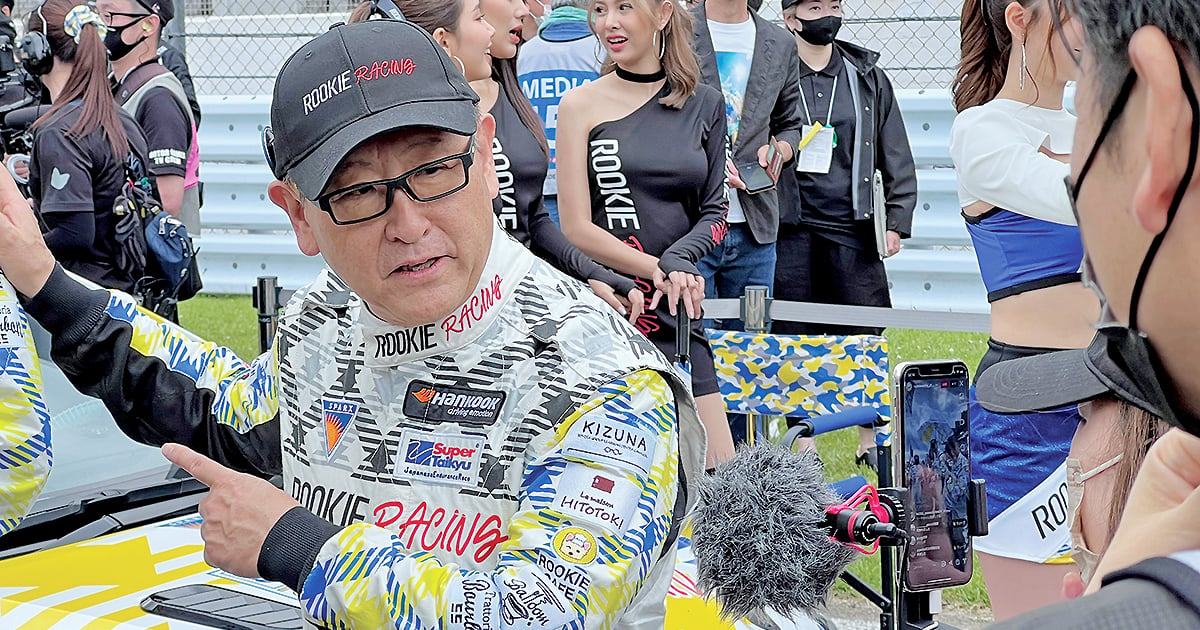
At first glance, Akio Toyoda seems woefully out of sync with today’s carbon-obsessed world when he fires up his GR Corolla race car and tears off down the straightaway at Fuji Speedway.
But even in an era all charged up about electrification, the Toyota Motor Corp. chairman insists his roaring, combustion-powered hot rod is just as gentle on the environment as any electric vehicle.
Why? Because its turbocharged 1.6-liter three-banger slurps up clean-burning, zero-emission hydrogen, not carbon-laden gasoline. Toyoda has been putting the technology through its paces since 2021 as his company joins an increasingly pitched global battle against carbon dioxide.
Automakers, suppliers, labor unions and governments may debate the best and fastest ways to mitigate emissions of this greenhouse gas and blunt its impact on the global climate. But there is one matter few disagree on, and the Toyota boss best sums up that zeitgeist: “Carbon is our enemy.”
Not long ago, the industry paid little attention to such buzzwords as “carbon neutrality” and “net zero.” Today, no boardroom PowerPoint presentation or corporate mission statement is complete without a plan of action for slashing carbon emissions from global operations.
Virtually every business and industry is focused on cutting carbon. But the transportation sector, which churns out 27 percent of U.S. greenhouse gas emissions and is the largest contributor to global warming, bears a special responsibility to spearhead the drive.
Carbon-cutting pledges from carmakers, suppliers and governments worldwide typically eye a 2050 timeline for zeroing out the amount of the greenhouse gas let loose into the atmosphere.
Advocates say achieving that target is necessary if the world is to have any hope of limiting Earth’s mean temperature increase to under 2 degrees Celsius (3.6 degrees Fahrenheit) by midcentury as outlined under the 2015 Paris Agreement on fighting climate change.
The movement has been galvanized by government regulation, international accords, shareholder activism, environmental campaigns and, in many instances, simply by the need to cut long-term costs, improve efficiency and stay competitive. The efforts hinge on a mix of reducing activities that emit carbon, switching to renewable energies and recycling as much as possible.
The urgency is most palpable in the auto industry’s rush to EVs.
In the U.S., where pioneer Tesla dominates the segment, EVs account for nearly 7 percent of light-vehicle registrations, rocketing up from just over 1 percent in 2019, according to data from Experian.
By the end of this year, about half of new-car buyers in the U.S. could at least find an EVat the price and size they want, and from their favored brand, J.D. Power predicts.
The EPA’s recent proposal to impose its strictest-ever limits on tailpipe emissions could further accelerate the mainstreaming of EVs. Under the plan, the agency projects that EVs could account for up to 67 percent of new light-duty vehicle sales in the 2032 model year.
But as Toyoda’s approach highlights, EVs are only one path to the solution. Other technologies also may play important roles in zapping carbon output from tomorrow’s vehicles. That could include using hydrogen in combustion engines and also fuel cell vehicles, as well as synthetic e-fuels and even biofuels.
Debate still rages over which is the best road to cutting carbon. Strategies vary according to technologies, cost, infrastructure and regional needs. EVs might catch on quickly in markets such as the U.S. or Europe, for instance, but much slower, if at all, in places such as India or Africa.
Indeed, the carbon conundrum stretches far beyond vehicles on the road.
By definition, the effort must focus on the factories churning out the cars. And to do that, it also must address multiple tiers of suppliers — down to the carbon emitted in the mining of raw materials and how the energy is generated to power the entire manufacturing process.
Add to that the carbon associated with shipping and hauling those products to market, and even the footprint of the dealerships that sell cars to customers.
It’s a tangled, complicated calculation, requiring delicate coordination among diverse industries spanning different political and economic entities.
The strategies being laid out affect everything from investment and hiring to global trade.
Companies are expecting to spend billions to realign businesses for a greener future.
“Carbon neutrality cannot be achieved by car companies alone,” Toyoda often says, highlighting the hurdles ahead.
“We must reduce CO2 emissions in all processes of producing, transporting and using energy. There must be more than one route to carbon neutrality.”
The challenges are immense, starting simply with the matter of measuring and tracking the carbon trail over the entire life cycle of an automobile — from the metal mines to the junkyard.
Companies are tackling that task, but the work has only just begun. As the industry approaches 2050, the anti-carbon crusade will require increasingly revolutionary technologies involving big advances in renewable energies, batteries and hydrogen production, not to mention new systems to capture, store and reuse carbon on an industrial scale.
Then there are the million-dollar questions: Is carbon neutrality possible in the timeline humanity has set for itself?
And will the responsible actions of a handful of industries and proactive governments be enough to meaningfully dent the global temperature surge?
The auto industry alone may not be able to win the global war against greenhouse gases. But the war most certainly can’t be won without the global auto industry doing its part.