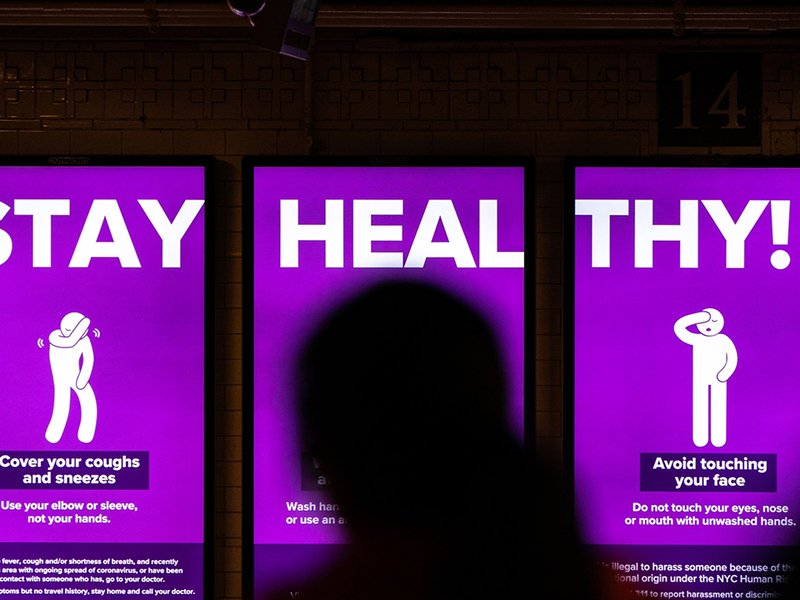
As automakers and suppliers prepare to restart North American production over the coming weeks, they’ll have more to worry about than just how to keep their parts supplies coming and how to keep their factories sanitized.
Among them: When the nation and the world are flying by the seat of their pants trying to deal with a deadly new virus, what is an employer’s liability exposure if something goes wrong?
Attorney Chris Reynolds — who also happens to be head of manufacturing for Toyota Motor North America — says the industry as well as other employers are about to discover the answer to that question.
“What is the liability standard for a situation that is unprecedented? We will surely find out,” Reynolds said as he laid out plans Thursday, April 23, for Toyota’s plants in the United States and Canada to return to limited production beginning May 4.
“Nobody has a good fix on it, if I put my legal hat on. But what our legal department and our health and safety groups are doing is, they are very carefully looking at the county-by-county, state-by-state and federal guidelines that apply to things like essential business activities; what that means, how people can undertake them and how people can comply with whatever guidelines apply to a given location.”
Reynolds said it can “sometimes require a lawyerly examination” of those guidelines, especially in cases where they might conflict. And in such cases, employers might find themselves exposed.
While its production across the U.S. and Canada has been suspended since March 23, and its roughly 29,000 production workers have been idled, Toyota has recorded 24 cases of COVID-19 infection among its work force, Reynolds said, including 13 individuals who have fully recovered.
Reynolds said despite taking huge steps to improve worker safety on the job and limit exposure among employees, it’s not realistic to assume there won’t be more cases.
“That number is going to change. This is not a situation where we expect zero cases. We just have to be realistic,” Reynolds said. He noted that Toyota plants in China and France have already returned to operations. “Believe me, we’ve been avidly following what they’ve been doing and how effective it is. We’re not letting that go to waste at all.”
The automaker has developed a best practices handbook to guide its return to production and is complying with the advice distributed by public health officials, Reynolds said.
“Right now, most of the energy is focused moreso on making sure that our own activities comply with what governments have been putting out and various authorities have been putting out with regards to what they want essential businesses to do, and not so much on liability.”
While the automaker has sufficient stores of parts on hand to start building vehicles once workers return to plants, Reynolds said Toyota would take time “to shake off the rust” with workers who haven’t been on the job in more than a month, and to implement and train workers in extensive new safety procedures that will both slow the run rates of assembly lines and hopefully help keep them safe.
“I would be surprised if a car rolls off a line anywhere on May 4,” Reynolds told reporters last week.
The new procedures — including staggering entrance and exit times to avoid crowding, altering workspaces to allow workers to be separate from one another and placing physical barriers to separate workers in close proximity — “are going to take some time, and we’re going to take the time.”