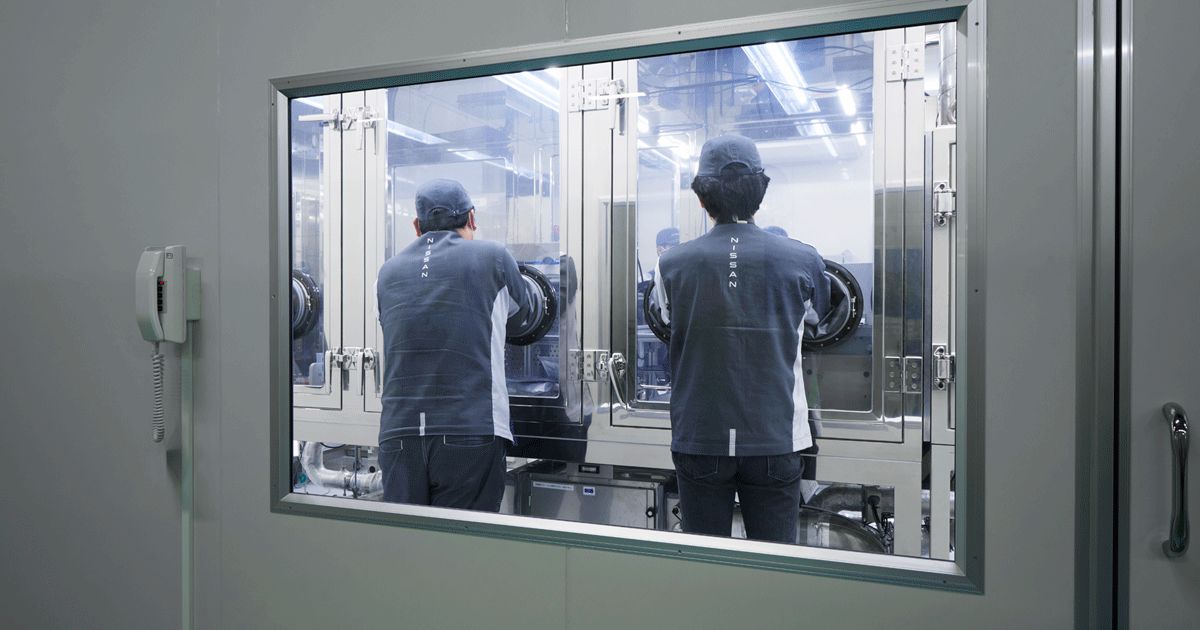
TOKYO — The engineering guru leading Nissan‘s quest for solid-state batteries wants to disabuse people of the notion that solid state is inherently safer than today’s lithium ion packs.
True, next-generation solid-state batteries don’t have a flammable liquid electrolyte. But they do cram in a lot more energy, and that could make for some unpleasant fireworks if something goes haywire.
“Energy density is double, so you have a potential bomb that’s more dangerous,” said Kazuhiro Doi, corporate vice president in charge of advanced battery research at the Japanese automaker.
“If a big accident occurs, it could become much more catastrophic than with today’s batteries.”
But Doi insists Nissan Motor Co. can now lick that safety problem and other key issues that make solid-state batteries difficult to deliver.
His team has been racing to solve conundrums as Nissan tries to deliver on its pledge to bring the lightweight, compact, energy-dense batteries to market in just six years.
The automaker believes it can deliver a battery that holds twice the energy of a lithium ion battery, charges in one-third the time and costs $75 per kilowatt-hour. Nissan also thinks it can whittle that cost to $65 before too long, achieving price parity with gasoline-powered cars.
The breakthrough, Nissan reckons, will enable it to roll out EVs in a swath of new segments, such as pickups, big SUVs and maybe even sports cars, where weight and size are issues.
“I think all-solid-state batteries can be a game-changer,” Doi said.
Right now, Nissan is taking only its first steps toward that goal, with a feasibility study laboratory where it is experimenting with the batteries in handmade, limited-run batches. But if all goes to plan, the small-scale, secretive workshop will lead to a pilot plant launch in 2024 and to mass-scale manufacturing in 2028.
Nissan is grappling with this important new technology as a host of startups and virtually every old-school rival, from Toyota and Volkswagen to General Motors, race to find the right road to success.
A peek inside Nissan’s laboratory shows just how long and arduous the road to solid state will be.
The 1,400-square-foot workshop is a walled-off dry room housed inside an old warehouse at Nissan’s Oppama factory complex where engineers once worked on prototyping new catalysts.
There, a group of 10 workers painstakingly mix an electrolyte slurry, scooping cathode powder from a plastic cup with a long spoon, by hand. They mix it into an inky black goop, which is spread like pancake mix onto thin aluminum sheets – only two cells at time.
After drying, the sheets go through a stamping machine reminiscent of a telephone booth that compresses them with three times the pressure used for standard lithium ion cells.
Workers then cut the electrolyte sheets to an appropriate size and carefully stack them with anode sheets. Finally, they vacuum-seal four-layer sets of cells into aluminum foil pouches.
The work is fastidious and time consuming. The bulk of the processes are done through plexiglass glove boxes to maintain ultralow humidity and cleanliness. Because the rooms are so dry, technicians are required to take hydration breaks every two hours.
Right now, Nissan’s laboratory churns out only about 50 of these four-layer pouches a month, says Kenzo Oshihara, deputy general manager for innovative battery production engineering.
Just one electric vehicle, he reckons, would need about 5,000 such pouches.
“It would take a very long time before we could make a battery for a car in this room,” Oshihara said. “The mass-production equipment will have to be more sophisticated.”
The challenge is in the know-how as well as the manufacturing. Nissan is still searching for the right chemistry of the cathode and anodes. It has a partnership with NASA that allows it to search the agency’s vast battery database for potent material combinations.
Using artificial intelligence to sift through formulas, Nissan believes it can slash research time by more than half, from a five- to 20-year timeline to just two or three years.
Nissan is also focused on a cobalt-free cathode chemistry that will probably use sulfur or manganese because those materials are relatively plentiful and inexpensive, Doi said. On the anode side, Nissan sees potential for silicon-based or lithium-metal compounds.
Then there are the exacting standards of manufacturing these cells.
For starters, the pancake mix slurry must be whipped so finely that it gets all the lumps out to maximize battery conductivity. The layers of cathode-electrolyte-anode need to be lined up absolutely precisely. Along the way, Nissan must perfect how to ramp up all this procedure to mass-production speeds.
“It’s all about precision, but precision has relevance to cost and speed,” Doi said. “Compared with traditional lithium ion, this is a much more complicated set of technologies.”
Nissan says it has already overcome several obstacles.
It has adopted a binder on the cathode that reduces resistance and improves the movement of lithium ions. Engineers have also identified a material that inhibits the formation of dendrites that can short-circuit the battery. They have also discovered a design that allows the electrolyte and electrode layers to expand and contract repeatedly without detaching.
And crucially, Doi’s team says it has cracked the trick of fast charging in low temperatures.
Despite a growing field of startups and suppliers trying to break into solid-state batteries, Nissan sees advantages of going it alone and developing them in-house rather than in partnerships, at least in the beginning stages.
“They don’t have mature technology that enables them to work with auto manufacturers like us,” Doi said of outside suppliers.
Nissan wants to control the know-how that goes into elements such as cell design and manufacturing, not necessarily the chemistry of the raw materials themselves.
“That will be the source of our competitiveness,” he said.
But Nissan has only a few years to figure out the formula and deliver the cost goals by its 2028 target. It expects to get there by using less expensive materials and streamlining its production processes.
“We’re talking about R&D, so there’s no such thing as 100 percent confidence,” Doi said. “But if we try hard, we can do it.”