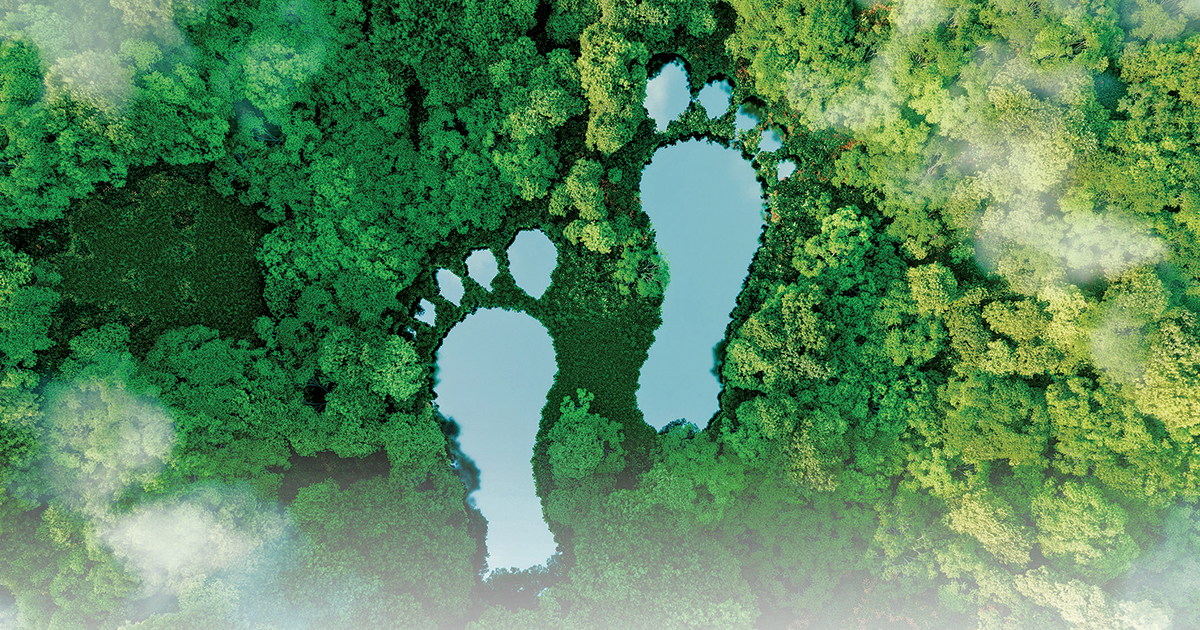
Under pressure from their customers to decarbonize, automotive suppliers are rethinking how they design, build and dispose of their products and are making changes to their operations so that they can become more sustainable.
The changes range from relatively small tweaks, such as installing more eco-friendly lighting in offices, to completely altering the types of products they build or where they build them.
Here are examples of how suppliers are changing their ways to become better environmental stewards.
Forvia, the world’s seventh-largest parts supplier, in November launched a brand, Materi’act, focused on the development and manufacturing of sustainable materials. It makes products ranging from green steel and sustainable carbon fibers to compounds created from recycled and bio-based materials. Those materials include an alternative to leather made of pineapple fibers, as well as compounds developed with hemp and its agricultural byproducts, according to Materi’act. Its products can be made with a carbon footprint up to 85 percent lower than comparable materials made today, Forvia said.
Forvia is investing heavily in the brand to meet automakers’ climate targets. A new R&D center is planned for this year, and it expects to hire about 400 people for Materi’act by 2025.
German supplier Continental has a long history of making tires. But the rise of electric vehicles and rapidly approaching climate targets are changing how it designs them.
Its Conti Urban concept tire, introduced last year and designed for city buses and for delivery vehicles for use in cities, is made up of about half renewable or recycled materials. The tire’s tread goes even further, with about 68 percent coming from renewable materials such as rapeseed oil, natural rubber and material gleaned from rice husk ashes. The development of more sustainable tires comes as Continental looks to build a supply chain that is completely carbon neutral by 2050.
Canadian parts supplier Martinrea International is betting that graphene, a material with properties that might sound straight out of a sci-fi novel, will revolutionize how key vehicle components can be more sustainable.
Graphene is a carbon-based material stronger than steel and more conductive than copper. Companies such as Martinrea believe its properties could make their products more efficient. The supplier uses graphene in new brake lines, greatly boosting durability and strength while reducing weight by up to 25 percent compared with a traditional brake line. Reducing weight reduces a vehicle’s overall carbon footprint.
In 2021, ZF Group moved about 750 employees into a state-of-the-art technical center in Solihull, England. There, they develop technologies related to electrification, autonomous driving, advanced safety systems and other key business areas for the German supplier.
The new center is notable not only for the advanced technology developed there, but also because it serves as a template for how other buildings can be designed to be more efficient and eco-friendly.
An innovative heat pump design, sophisticated sensors, LED lighting and other solutions helped ZF Group to use 75 percent less gas and 20 percent less electricity than the building it replaced, the company said.