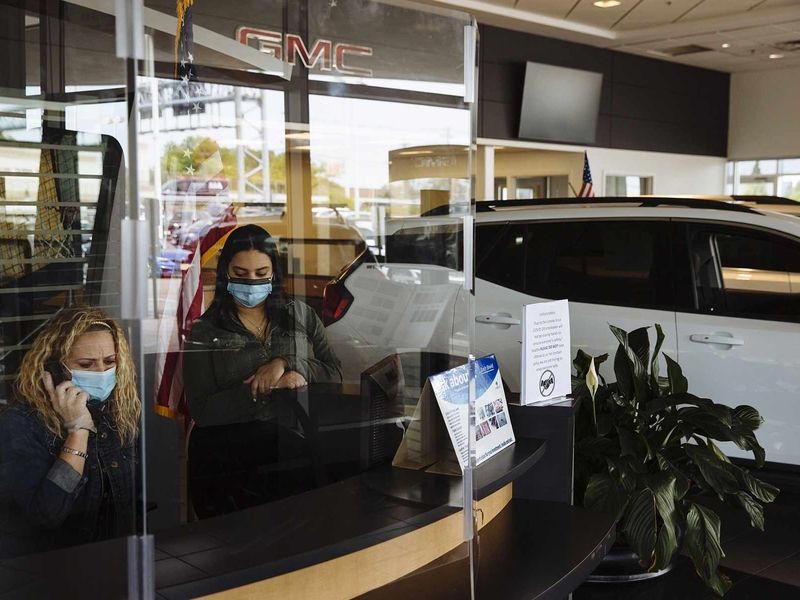
DETROIT — General Motors reported a $758 million second-quarter loss as the coronavirus pandemic sharply cut production and revenue by more than half.
GM said cost cutting and strong pricing allowed the automaker to nearly break even in North America despite its plants being closed for eight weeks.
GM lost $101 million in North America, compared with a gain of $3 billion in the second quarter of 2019.
“These results illustrate the resiliency and earnings power of the business as we make the critical investments necessary for our future,” CFO Dhivya Suryadevara said in a statement Wednesday.
Global revenue fell 53 percent to $16.8 billion, and its adjusted loss before interest and taxes was $536 million, compared with $3 billion a year earlier. The company burned through $8 billion in automotive operating cash but said it still had “strong” liquidity of $30.6 billion after borrowing $16 billion in March to help weather the crisis.
GM’s international regions lost $270 million in the quarter, compared with a $48 million loss a year earlier, and China equity income fell by $66 million to $169 million.
Earnings from GM Financial decreased 58 percent to $226 million.
GM’s loss of $464 million so far this year compares with net income of $4.6 billion in the first half of 2019.
Shares of GM fell 0.5 percent in early trading after gaining more than 4 percent in premarket trading.
GM told salaried employees Wednesday that it will stop deferring 20 percent of their pay and give them the missed earnings later this year, rather than in early 2021 as it had planned. GM previously said the salary deferrals, which started April 1 as a way to conserve cash, could last for six months.
“GM deserves credit for pivoting quickly and rolling out blockbuster incentive programs that arguably kept the industry afloat through its most challenging period in more than a decade,” Jessica Caldwell, Edmunds’ executive director of insights, said in a statement.
“With the worst quarter now behind GM, the company — like all automakers — is challenged to sell in a world filled with uncertainty for consumers, employees and operations.”
The company reopened North American plants in mid-May after closing them in March to curb the spread of the coronavirus. Many dealerships around the country also closed or limited hours and services because of the pandemic.
GM’s U.S. light-vehicle sales sank 34 percent in the quarter because of the pandemic’s effect on demand and tight inventories at dealerships. Its North American plant capacity utilization rate, based on two shifts, plunged to 36 percent in the second quarter from 104 percent a year ago.
The automaker now requires plant workers to maintain physical distancing, wear face masks and safety glasses, and participate in health questionnaires and temperature screenings.
Repaying debt
GM said it remains on track with the restructuring plan it launched in 2018. In the second quarter, the automaker got about $200 million closer to its cost-reduction goal.
Suryadevara said that as long as the economy continues to recover, she expects GM to pay back the additional debt it incurred in response to the pandemic by the end of the year.
GM is not providing financial guidance for the second half of 2020, but Suryadevara said in a 14-million-unit industry with no disruption to production, GM expects $7 billion to $9 billion in cash generation, which would help repay debt and offset the cash burn in the first half of the year.
“We’re watching the virus, the economy and its impact on the overall industry very closely,” she said on a call with reporters. “But the takeaway for this quarter is our ability to flex our cost structure quickly and to preserve liquidity and demonstrate the performance that we’ve been working towards over the past few years. And we will continue to do that and continue to be laser-focused across all areas of the business.”
Pickup sales
Full-size truck sales were flat in March, April and May, despite a dip in overall demand, Suryadevara said. In June, sales decreased because of dwindling inventory, but July sales were flat year-over-year, she said.
“It really shows the resiliency of that business,” she said.
GM will increase regular production of light-duty full-size pickups at its Fort Wayne, Ind., plant by about 1,000 units per month starting Sept. 1. That would be about a 4 percent boost from the estimated 25,707 pickups the plant built in June, according to the Automotive News Data Center.
Through July 25, GM dealers’ inventory has increased 9 percent, and the number of vehicles in transit has risen 6 percent since June, GM said. Total inventory was about 480,000 units as of July 25. By the end of the year, as long as the economy continues to recover, GM expects to have 600,000 units of inventory.
“We have made some progress, but we have more to do. By the end of the year, there should be a healthy rebuild,” Suryadevara said. “And from there, we’re going to look at what the demand situation is.”