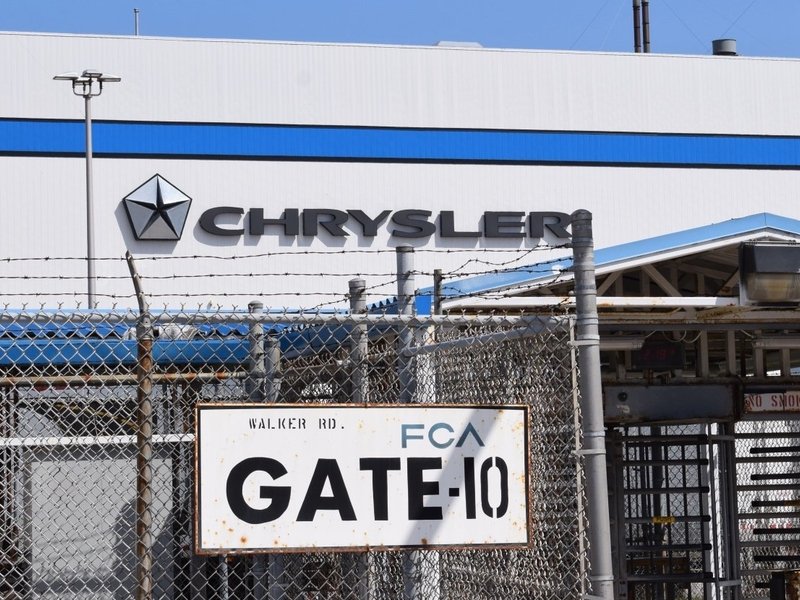
As automakers eye a return to production, FCA Canada says it is taking steps to keep its factory employees safe on the shop floor.
Some employees are currently working at the automaker’s Canadian assembly plants in Windsor and Brampton. They’re deep cleaning the facilities and tweaking job stations to make room for social distancing. But those that arrive for work each day no longer simply swipe their time card and walk into the factory as they used to.
FCA Canada spokeswoman LouAnn Gosselin told Automotive News Canada that employees are now required to wear face masks and gloves.
“Employees also will be asked to complete a wellness self-assessment at home each day before reporting to work. This includes taking their temperature and answering five survey questions,” Gosselin said in an email.
FCA on Monday said said that it “intends to progressively restart its U.S. and Canadian manufacturing facilities beginning May 4.”
“During this current production pause, we are working with government officials and our unions to implement new procedures to certify the daily wellness of our workforce while also redesigning work stations to maintain proper social distancing and expanding the already extensive cleaning protocols at all locations,” the automaker said in a statement April 6. “As a result of these actions, we will only restart operations with safe, secure and sanitized workplaces to protect all of our employees.”
FCA Canada currently builds the Chrysler Pacifica and Voyager and Dodge Grand Caravan minivans in Windsor. In Brampton, just outside of Toronto, it builds the Dodge Charger and Challenger cars and Chrysler 300 sedan.
Reuters on Thursday reported that safety measures differ from manufacturer to manufacturer. For example, Ferrari said on Wednesday it would offer voluntary blood tests to employees who wanted to know if they had been exposed to the virus.
Most automakers, including FCA Canada, are converging on a consensus that temperature screening, daily health questionnaires, assembly lines redesigned to keep workers three to six feet apart, and lots of masks and gloves can enable large-scale factories to operate safely.
At General Motors’ ventilator assembly plant in Kokomo, Ind., workers and managers have been fine-tuning details such as when employees are handed masks, and when they step in front of a temperature screening device.
Initially, ventilator assemblers in training at Kokomo walked down a hall before getting a mask, said Debby Hollis, one of the UAW-represented workers. Last week, she said, “They met us at the door and had us get in the masks there.”
The time workers spend putting on extra protective gear, the time spent doing extra cleaning, and spreading workers out on assembly lines designed to have one vehicle roll off the end every 60 seconds could undercut productivity.
“If we can protect employees, we can get work done,” said Johnson, the GM manufacturing chief. “The magnitude of the incremental cost is irrelevant. Costs will be managed.”
Reuters contributed to this report.