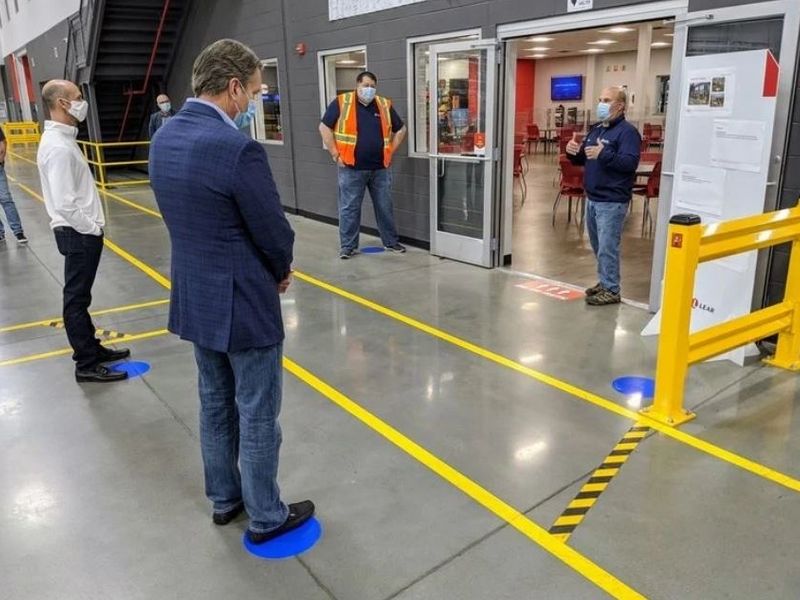
FLINT, Mich. — I stepped out of the rain into a black tent where a masked man thrust a pair of grill tongs my direction.
Pinched at the end was a fresh basic surgical-grade mask. A thumbs up signaled to the next masked man that I had not knowingly been in contact with a person infected with COVID-19, nor was I experiencing any symptoms. My temperature was taken and I was permitted to enter the facility.
I returned to work Thursday. Not my Crain Communications Inc. office in Detroit, but Lear Corp.’s just-in-time seating plant on Flint’s historic Buick City site.
The automotive seating supplier held an open house, of sorts, for its production line leaders to get them acclimated with the rigorous new safety protocols as the plant is set to begin limited production Monday.
Admittedly, walking into a production plant in the middle of a pandemic that’s claimed the lives of nearly 86,000 Americans in the last 100 days is nightmare fuel. I was fearful — for my safety and the safety of my family.
But Lear published its “playbook” for reopening on April 6 — several companies have since published their plans — and more than a month later, I was offered the chance to witness and report on its implementation in person. Fear be damned. The opportunity for unfettered access and a plant tour with Lear CEO Ray Scott and his team of production leaders (the interview with Scott will be published in Monday’s edition of Crain’s Detroit Business, an affiliate of Automotive News) proved too juicy for my journalistic lizard brain to decline.
Once inside, the Flint factory is largely the same as all modern manufacturing plants, organized and surprisingly clean. But the first thing workers will notice on Monday is an overabundance of signage, directing them down now one-way paths and blue circles on the floor neatly spaced 6 feet apart anywhere people may congregate. There is one way in and one way out of bathrooms, cafeterias and up and down stairs. Workers are instructed via orange dots on every sixth step how to maintain distance. Masks are required.
Drinking fountains are also shut down, save for the water bottle filling stations. Sanitizer is everywhere, at least two within eye shot at any point in the plant. In the cafeteria, each four-person table is outfitted with quadrant of plexiglass, blocking respiration of unmasked employees as they eat. As Scott and the rest of the Lear crew meandered through the cafeteria, I politely interrupted two production line leaders to ask how safe they felt. They both indicated they felt comfortable and I asked one of them to explain.
“I came in shaking my head, but the level of thought they put into safety made me comfortable rather quickly,” she said. “It’s certainly safer here than the grocery store.”
That’s a sentiment I overheard as I passed several employees on my tour. Granted, it’s important to note only about 50 of the plant’s 675 employees were present Thursday. The plant will restart Monday with only one shift of about 225 employees.
I’m known to have a bit of a potty mouth and throughout this idea of returning to work my biggest concern has been, and will always be, the toilets. I have asked at least a half dozen experts about bathroom protocols in the last week alone.
At Lear’s Flint plant, every other urinal (I only went into the men’s room) is covered in orange tape, as well as the sinks.
Workers are instructed to maintain distance as they enter, use the restrooms and wash up. Scott mentioned to Frank Orsini, president of the supplier’s seating division, that turning the water off at the cordoned off sinks was important as workers at its Tuscaloosa, Ala., plant had used them anyway in a rush to get out of the restroom. Toilet stalls did not appear to be limited in any fashion.
A more rigid cleaning schedule is also now a priority. In fact, cleansers and supplies are located on carts throughout the plant. Orsini said one worker per every 12-14 employees is dedicated to sanitization.
The second-floor conference rooms and office space have also changed. No more than 10 people are permitted in a conference room and extra partitions were added between cubicles.
But the main show at the plant is the seat production and work stations that were adjusted to meet the company’s new protocols. Plexiglass dividers were added between work stations and work flows changed to provide optimal distancing. That, of course, comes at a cost.
Scott declined to discuss the costs associated with all the new safety measures, but efficiency is certainly slowed.
Orsini indicated on the tour that production will likely slow from 16 seats per hour to only 12.
Scott quickly said, “I don’t care about volumes right now. Let’s get this (safety) right.”
Maybe that’s just a peachy line to say in front of a reporter, trying to prove the health of Lear’s employees are more important than profits.
But I didn’t get that sense from Scott. He mentioned more than once when I was near out of earshot that he’d push back on the customer — the Flint plant supplies complete seats to GM’s Flint Assembly a mere five miles away — if safety protocols were not working or compromised in order to meet demand. Scott also recognizes the well-being of employees is directly related to profits long-term. An outbreak of COVID-19 shuts down production, too.
Scott and Lear appear to be committed to solving the pandemic puzzle as well as easing employees’ minds. During the open house Thursday and potentially into next week, the company was offering on-site antibody testing to its employees. A staff of four from Beaumont Health operated the testing — a serology test determines whether the patient has had COVID-19 and whether they now have antibodies against the virus.
Crain’s Detroit Business reporter Jay Greene has written about his own experience with the antibody test in recent weeks.
As Greene notes, as of now the antibody tests are experimental and can’t determine whether COVID-19 antibodies mean a person is immune to the virus … yet.
Scott hopes the tests could in the future allow the company to improve efficiency and protocols if it knows who is and who is not immune, but acknowledges the limits of the testing. But he said even if it’s just data collection for the health sector, he’s happy to provide it to patients.
He already got his antibody test and insisted I do as well … for the greater good or maybe just peace of mind.
So, there I was, in the middle of an automotive manufacturing plant in Flint, getting blood drawn in the throes of a global pandemic.
I felt safe. From my very limited point of view, the protocols and processes at the plant seem about as safe as one could hope to be while producing automotive seats in the current environment.
I’ll find out if I have COVID-19 antibodies in the next two to three days and will know just how safe I was at the plant in the next two weeks.