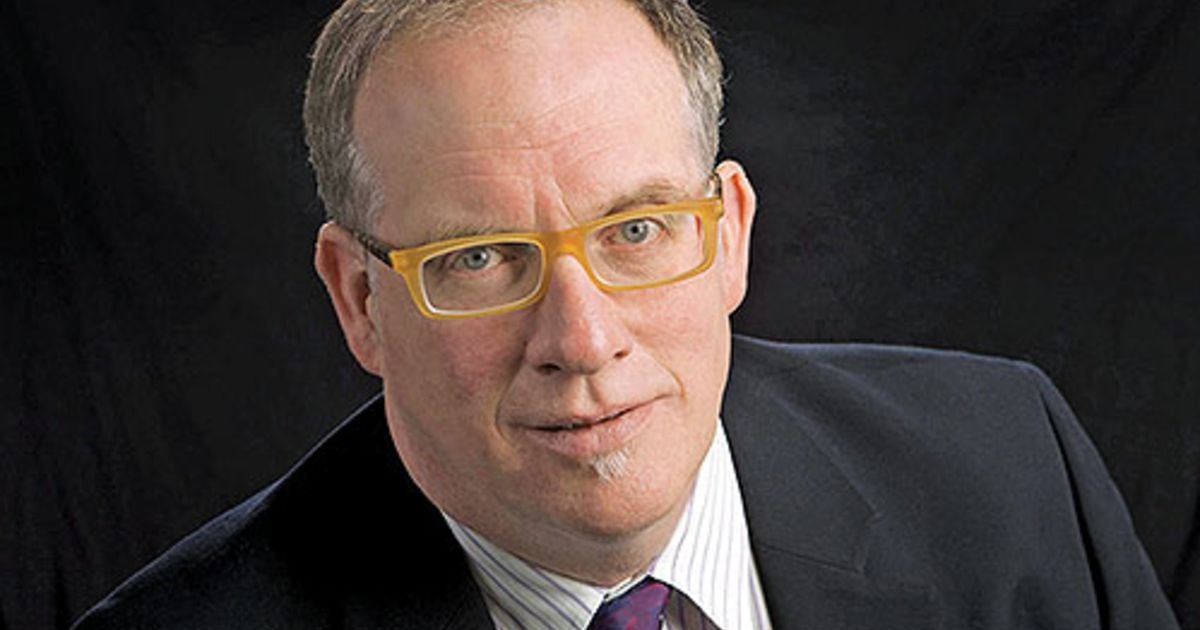
You implement a brilliant plan — and sometimes the results might be more complicated than you intended.
We tell you this week about a series of what you might call, for lack of a better name, unintended consequences.
John Irwin reports on the outlook for the UAW’s contract talks this year with the Detroit 3 — specifically on how they might sting the industry’s supply chain. His story reminds us that the last contract season in 2019 resulted in a 40-day strike against General Motors. And that development, in turn, caused thousands of parts maker layoffs and whacks to supplier earnings to the tune of hundreds of millions of dollars. His story makes the point that, this time, suppliers as a whole are not in a good place for a repeat. Since 2019, the sector has been buffeted by costly business interruptions caused by the pandemic and the microchip shortage. Even though the union is itching to set things right with the Detroit 3 on wages and job security this year, it’s probably not intending to further weaken the automakers’ supply base.
Nissan is also facing some unintended consequences, Urvaksh Karkaria reports. The automaker is building back steam on its factory output of its lower-end models, the Sentra, Versa and Kicks. And dealers are eager to get them. Those cars are a sweet spot for Nissan sales as customers cope with the rise in lending rates. But Nissan first has to honor some big commitments it has with fleet customers for the models. So a lot of the newly available product is going to rental lots instead of retail lots, and driving up the fleet share of Nissan’s business at a time when the company is determined not to lean on fleet sales like it used to.
Another case of “This isn’t what we had in mind” is occurring at EV startup Rivian. Laurence Iliff reports that Rivian is changing direction on the electric motors it uses in its trucks. Rivian was a bold illustration of how a startup could get off the ground by sourcing advanced technology from outside suppliers. But in Rivian’s case, those motors happened to require certain microchips that have been hard to get, and so its factory volumes have been lagging and the financial world has begun to doubt the startup’s manufacturing ability.
So Rivian is now switching to a new motor that it will manufacture itself inside its assembly plant, which should free up vehicle production. It’s not the original plan, but sometimes you have to pivot.
That’s the way it works in the car business. Things unfold in a different way. You go with it.