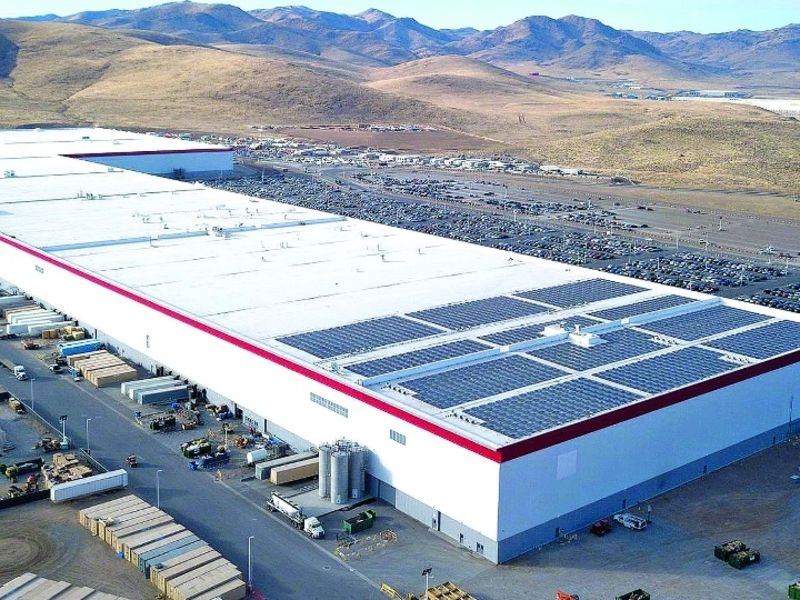
Panasonic Corp. has spent the past six months developing a battery cell with higher energy density and better fast-charging performance.
But taking an electric vehicle battery to a new level requires more than a tweak, said Celina Mikolajczak, vice president of battery technology at Panasonic Energy North America. The current innovation involves changes in design, materials and manufacturing processes.
“People like to envision a cell as kind of a commodity product,” Mikolajczak said. But a lithium ion cell is not a commodity product, she told Automotive News.
“Every design has its own challenges. It has its own strengths. It has its own demerits. I make a cell that’s optimized for one customer, a different customer wants a different optimization,” she said.
The product in question, known as Panasonic’s 2170 cell, supplies power to the Tesla Model 3 and Model Y batteries that are made at the Gigafactory in Reno, Nev., in which Panasonic and Tesla are partners.
Advancing the cell required a shift in design, which Mikolajczak said is more difficult to manufacture.
“Every time you do something new on the chemistry side, there’s always implications on the processing side,” she said.
“It’s been pushing a lot of our materials to their physical limits, and that becomes evident when you try to do the manufacturing at the scale that we manufacture at, and at the speed that we manufacture at,” she added.
“One of the things that made Tesla unique compared to the other automakers is their very rapid design cycle and modifications.”
Tesla’s fast-paced development cycles require hand-in-hand changes by Panasonic.
Panasonic is attempting to introduce new materials that are less expensive, including cobalt. Cobalt mining is also facing growing social disfavor, with critics targeting mines in the Democratic Republic of the Congo as unsafe.
“We’ve got to innovate a lot with our materials, supply chain and minerals extraction,” Mikolajczak said. “We’ve only scratched the surface of what is appropriate for minerals extraction and what can be done in a socially and environmentally appropriate way.”
Exchanging cobalt for nickel makes a lithium ion battery cell’s crystalline structure more sensitive to moisture and contaminants. That will require the manufacturing to move into dry-room production environments.
Panasonic is also considering advances in separators, for safety and reliability, and in nonactive materials such as copper foils, aluminum foils and cell cans.
“All of these are very engineered materials that have to sustain high-speed manufacturing processes,” the executive said. “Then they have to be reliable again in a car for eight years or longer.”
Mikolajczak said battery packs, battery manufacturing processes, battery fast-charging capabilities and the materials supply chain all have room for improvement across the industry.
Panasonic wants to make improvements in cell manufacturing that will yield better cell cost, quality and safety.
“For our factories, we can continue to push the limits of automation,” she said. “It’s a lot of machine design, a lot of big data analysis using AIs to do quality checks.
“It’s not battery chemistry, but it is really advanced manufacturing techniques.”