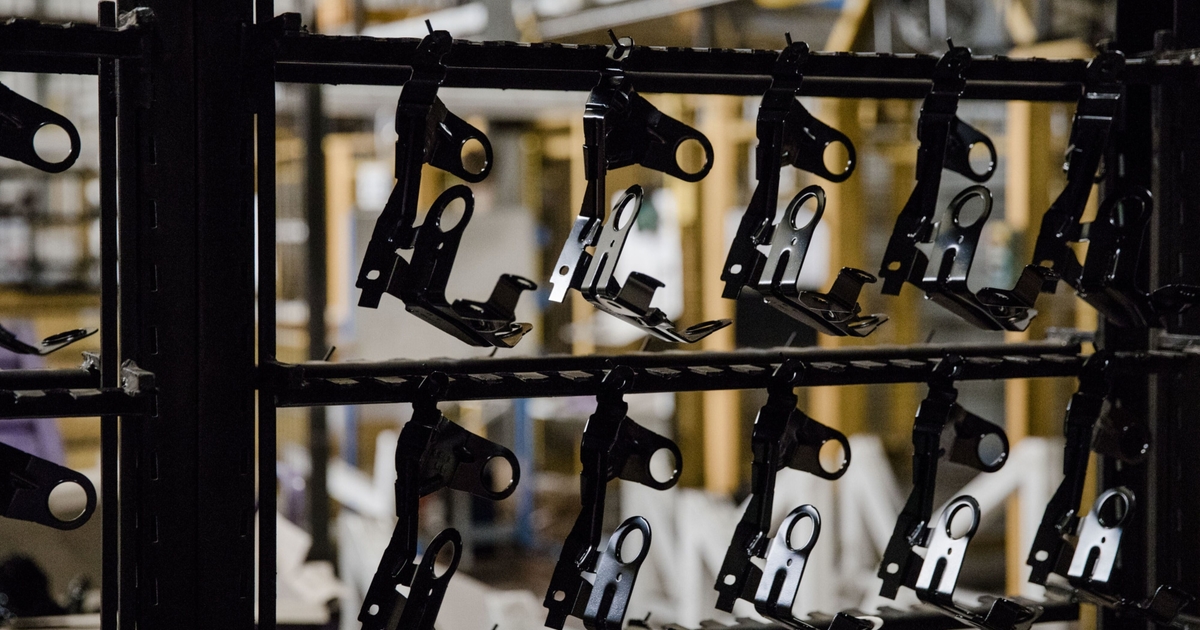
Chinese car parts makers are facing growing pressure from overseas customers to set up factories outside the country as mounting trade tensions and three years of COVID lockdowns make them wary of relying too heavily on China.
Carmakers from Europe and elsewhere are making direct overtures to manufacturers of everything from cooling components to brake systems and auto charging parts, pressing them to establish plants in places like Vietnam and Indonesia so they can still benefit from their expertise and long-held relationships but avoid the risks China poses right now, according to a number of suppliers interviewed by Bloomberg News.
While some international names like Airbus SE and Tesla Inc. are doubling down on Asia’s biggest economy, the shift is an increasing threat to China’s status as the world’s factory and its bid to regain the trust of global business amid the unpredictability of President Xi Jinping’s rule.
For one manager at a Jiangsu-based maker of electric-car charging components, the pressure is crystal clear. When his key European client visited for the first time after China ended its COVID Zero restrictions, the first thing he asked about was the company’s plans to set up an overseas plant, voicing his concerns about rising tensions between China and the West.
On the taxi ride from the airport to the factory, the manager and his client agreed to visit Vietnam and Thailand to scout for opportunities. “I don’t even like taking planes,” said Wang, who asked to be identified by only his surname so as not to reveal his employer or main customer. “But it looks like I have no choice. Move out, or lose the business.”
It’s not just auto parts makers feeling the pressure of what has come to be known as China+1: the push to establish at least one factory outside the home base of China. Most notably, Apple Inc. and its suppliers are moving production out of the country. Foxconn Technology Group plans to invest about $700 million on a new plant to make iPhone components in India, while AirPods maker GoerTek Inc. is plowing an initial $280 million into a new Vietnam facility and considering expanding in India.
“Firms are moving away from a cost-driven strategy to a resilience-driven strategy,” said Ben Simpfendorfer, a partner at Hong Kong-based consultancy Oliver Wyman. “The resilience is by adding an extra factory or more in a different part of the world,” he said, adding that the pandemic and trade tensions have brought into sharper focus the fragility of global supply chains.
China’s Sunrise Elc Technology Co., which supplies electrical components to German auto parts maker Robert Bosch GmbH and Japan’s Panasonic Holdings Corp., has already established a plant in Vietnam that makes set-top boxes for the consumer market overseas. On top of speeding up plans to acquire related credentials to produce auto parts in the Vietnam factory, it’s seeking sites in Europe and the US.
The overseas expansion has mainly been driven by the “fast-changing international situation,” Sunrise Chief Marketing Officer Timothy Huang said, referring in particular to China’s trade and political tensions with the US. Some policies implemented during the trade war, such as increased tariffs on a variety of Chinese goods, have now become normalized, Huang said in an interview from his office in Shanghai.
“What happened to consumer electronics is likely to be repeated in the automotive chain,” he said. The shifting out of auto parts will “just be a matter of time,” especially after Covid and lockdowns in key manufacturing hubs crippled the supply chain.
For the first time in about 25 years, China isn’t a top three investment priority for a majority of U.S. firms, an American Chamber of Commerce in China survey showed. The survey also found the proportion of companies moving supply chains elsewhere, or considering doing so, had almost doubled from a year ago.
With the challenges of doing business in China mounting, the European Chamber of Commerce in China said some of its members and their suppliers and partners have begun to make investments in other markets as they seek to build supply chain resilience. A survey it conducted last year showed that 23 percent respondents were considering shifting their current or planned investments out of China, the highest on record.
Minth Group Ltd., which makes structural body parts for cars along with decorative components and interior trims, last year signed an agreement with Renault SA to set up a joint venture to make battery boxes at a plant in Ruitz, France and broke ground on a factory in Poland that it will operate with Sanhua Holding Group Co. Those add to factories in Thailand, Germany, Serbia, the Czech Republic, the UK, Mexico and the US.
“We’ve all seen some recent trend of reverse globalization,” Liu Yanchun, Minth’s chief operating officer, said at an event in Shanghai in February. Other factors behind the shift include growing restrictions on Chinese exports ushered in by President Joe Biden’s Inflation Reduction Act — which aims to reduce reliance on Chinese materials, particularly in electric cars. U.S. automakers are also favoring more local suppliers, and clients are demanding faster response times to fill orders.
By spreading production facilities around the world, Liu said Minth would be better placed to deal with client needs and geopolitical risks such as trade tensions or the outbreak of war.
“We’ll have many cards to play, and will never be checkmated,” he said.