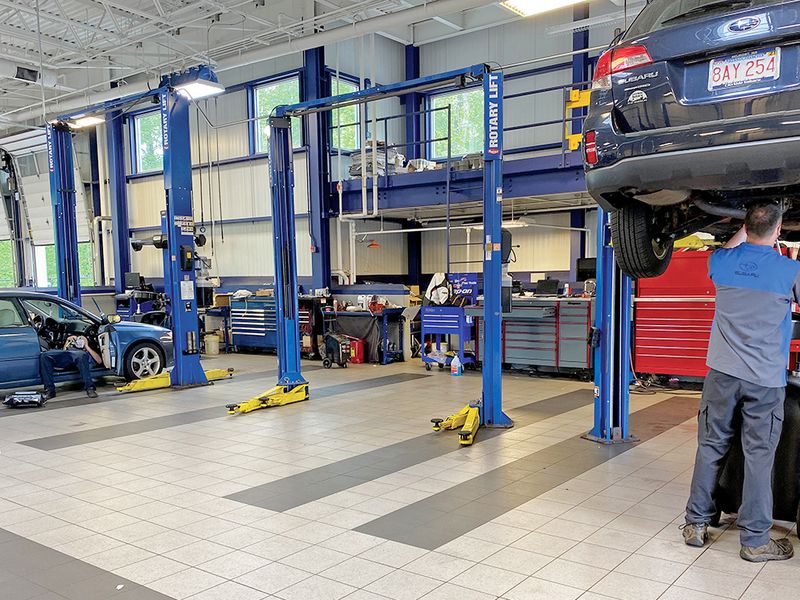
In the “new normal” world imposed by the COVID-19 pandemic, technicians at Patriot Subaru of Saco, near Portland, Maine, now work firefighter shifts — three 11-hour days a week. Plus they work only in every other bay to maintain social distancing.
And at Hansel Auto Group in California, technicians now diligently — not occasionally — video record their multipoint walkaround inspections to better communicate virtually with customers.
As these changes show, furloughed fixed ops employees who return will likely find their jobs are quite different from the ones they left. Furthermore, the work will demand new skills and mindsets, including more technical proficiency and an ability to adapt to change.
“Yesterday’s normal is never coming back,” says Adam Arens, CEO of Patriot Auto Group, which operates three rooftops in Maine, Massachusetts and New Hampshire. “That’s why we’re diligently looking way down the road trying to figure out what kind of people and processes we need for the future.”
David Long, executive general manager at Hansel, says almost everything will be done from a distance — from customer engagement to walkarounds. He says the pandemic has forced Hansel dealerships to alter operations in ways that customers have wanted for a while.
“Now we have to do it, not just think about doing it,” says Long, who oversees Hansel’s eight dealerships in Santa Rosa and Petaluma. “Employees need to understand how this business now has changed exponentially. With COVID-19, we’ve gone from a crockpot mentality, where we’ve slowly made minor changes, to a microwave mentality, where changes are almost instant.
“Employees will need to adapt quickly.”
Rick Wegley, an instructor at the NCM Institute run by NCM Associates, an automotive consulting and training firm, agrees that willingness to change will be a key employee attribute going forward.
“Employees may be asked to do things they’ve never done before … they’ll have to adopt a whatever-it-takes attitude,” he says. “Look at it this way: If you don’t like change, you’re going to hate extinction.”
Bruce Gamble, owner of Acme Automotive Training, says fixed ops employees should get used to wearing more than one hat.
“They’ll need to embrace cross-training so things can keep going when other people are out, either from COVID-19 or something else,” he predicts.
As examples, service advisers might have to double as car jockeys or cashiers. Parts desk employees may have to handle retail customers as well as keep technicians supplied, Gamble says.
“Just like a Boy Scout, they’ll have to be prepared,” he notes.
There are some positives with the changes. Wegley says some of his clients report their employees are more engaged in the wake of downsizing. Others report upticks in fixed ops productivity and revenue per repair order, perhaps because advisers have more time to sell additional services since customer traffic is down.
Gamble believes higher-revenue repair orders will become a larger trend because technicians have more time to inspect vehicles.
“With reduced [fixed ops] traffic, technicians have an opportunity to take a more detailed look at cars,” he says. “Plus customers are more willing to do things now as opposed to waiting until later because they don’t want to have to bring their vehicle in for a second time.”
Arens says he already had dabbled with three-day shifts at the Subaru store in Maine, which has 20 service bays, before the coronavirus pandemic. The group has another Subaru store in Massachusetts and a Nissan store in New Hampshire. It is building an Acura dealership outside Portland.
He went all-in on the concept when social distancing protocols forced technicians to work in every other bay.
“If we can only have half as many technicians working at one time, we need to maintain production without having technicians under a car for eight or nine hours, five days a week,” he says. “Plus, we want to keep as many techs working as possible so we don’t lose them.”
So far, the results are promising. Arens says technicians that were producing 80 hours of flat-rate work during a five-day, roughly 45-hour week before the pandemic now churn out 70 hours of flat-rate work in 36 hours.
That may sound counterintuitive, but Arens explains that technicians start a day out slow and end it slow as they begin to clean about an hour before a shift ends. They also take an hour lunch break. Now there are only three days with those inefficient periods instead of five.
“So they’re more efficient, even though they’re working fewer hours,” he says. “Techs that initially said no to it now love it.”
At Hansel, which at peak level had furloughed about 170 fixed ops employees, Long expects most workers to come back. But they’ll need to be attuned to treating every customer the way they want to be treated. That may mean wearing masks, using more technology to maintain social distancing or picking up and dropping off vehicles at customers’ homes, he says.
“As such, we need incredibly nimble employees that can pay close attention to consumers’ preferences,” Long explains. “We can be tone-deaf and just sort of lean in, thinking this is temporary. But I don’t think that’s the case.”