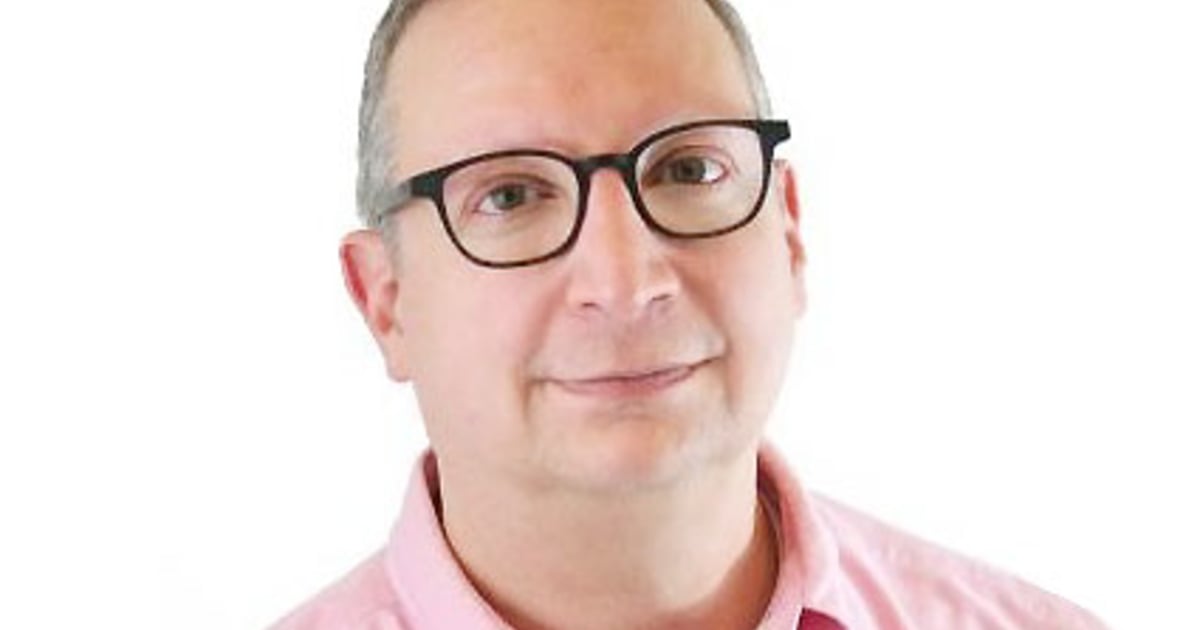
Google “FMEA” and you’re likely to find a variety of definitions. Risk assessment tool. Process methodology. Predictive failure analysis. It’s used as a noun, a verb and an adjective. So, what is it and why does it matter?
Failure mode and effects analysis is a process methodology created to help manufacturers and suppliers perform risk analysis and meet product, process and safety performance requirements. It ensures that potential problems are considered and addressed throughout design and product development to identify where they may happen, prevent them from happening and mitigate their impact.
Created in the 1940s by the U.S. military, FMEA provides manufacturers with a predictive step-by-step approach to identify all possible failures in a design, manufacturing or assembly process or product. Fast forward to the 1970s, when Ford Motor Co. introduced FMEA to the automotive industry for safety and regulatory consideration in the wake of its Ford Pinto scandal. The vehicle’s fuel tank was located just behind the rear axle, and with a slight bump it would catch fire. This led Ford to embrace FMEA to improve the safety, design and production of all its vehicles.
Today, many of the largest global automotive companies embrace FMEA, with some even requiring suppliers to adhere to its qualitative design, process, system monitoring and response steps. It enables manufacturers to identify the parts of a process that need changing; helps design engineers look for specific failure points in a system; helps manufacturing engineers design better processes; and helps suppliers understand where unique failure modes might exist in their supply chain. It’s comprehensive and rapidly gaining acceptance as an industry mandate.
When the Automotive Industry Action Group was formed in 1982, it pushed automotive companies and suppliers to agree on standards for quality improvement methods, including FMEA. Today AIAG and VDA: The German Association of the Automotive Industry are driving the universal adoption of FMEA standards, ensuring that automakers, suppliers, service providers and government entities work collaboratively to increase safety and quality and drive down costs across the automotive supply chain.
What started in the automotive industry to predict and prevent failures in design and production processes is now being adopted by other industries to identify to assess potential problems and their impact. In the aerospace industry, for example, FMEA is being used to assess aircraft safety risks. In health care, it’s being used to identify and mitigate risks that could potentially harm patients.
Automotive, aviation and other discrete manufacturers, such as Ford and BMW, are moving toward requiring compliance with the AIAG-VDA FMEA standard. Suppliers that don’t adopt the standard risk future work with manufacturers.
FMEA defines how to look at discrete effects of a failure and how those failures impact customers and the supply chain. When there is a failure mode, it drives a CAPA or a nonconformance, which may include a notice to customers about their warranties. Its impact reaches across the entire enterprise.
As with any process, the FMEA methodology has evolved. Today, there are seven steps as defined by AIAG-VDA standards.
1. Planning and preparation: Determine which process, system, metrics or aspect of your business you need to focus on.
2. Structure analysis: Identify and break down the design into the system, subsystems, assemblies and component elements.
3. Function analysis: Explore what the product should be doing and how that functionality is facilitated.
4. Failure analysis: Explore any element that could fail to meet its intended function.
5. Risk analysis: Evaluate the severity, occurrence and detection of each failure chain.
6. Optimization: Develop actions that reduce risk and increase customer satisfaction by improving the product.
7. Results documentation: Document the results of each FMEA investigation.
Traditionally, the planning and analysis of cause and effect of failures were mapped out manually on Excel spreadsheets. While still the primary tracking tool for many manufacturers and industries, this manual method has significant limitations, such as the inability to illustrate the interrelation between all the processes and parts; how a change in one process can impact another process; or how to highlight the common causes of failure — not just with one discrete part, but across a family of components or across a division or an organization.
Because of its inherent need for information across the enterprise, when FMEA is integrated within a quality management systems workflow, it is supported with automated compliance, risk management, document control and employee training capabilities. By tracking all possible failure points with FMEA, root-cause analysis is simplified, ensuring better quality planning decisions and reducing the time required to study failure effects and their mitigation.
The mandated use of FMEA as a critical methodology is expanding beyond automotive markets, empowering manufacturers and their suppliers with new ways to mitigate risk and ultimately build safer, quality-driven products.