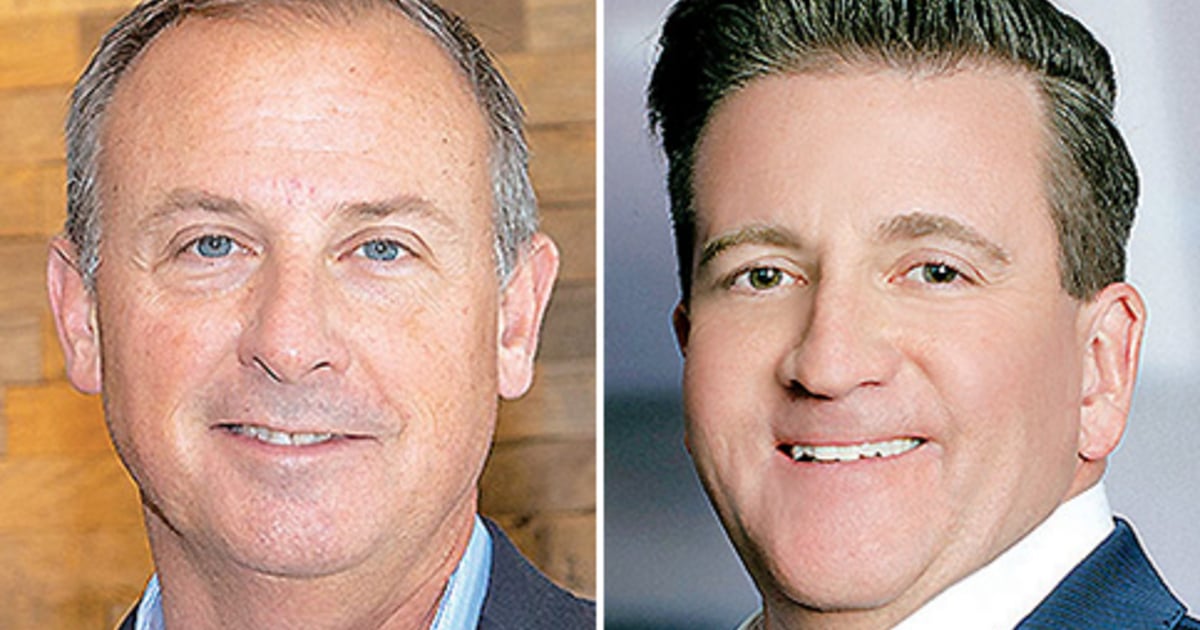
Electric vehicles are complex pieces of machinery made up of roughly 30,000 parts. As both the public and private sectors look to accelerate the adoption of EVs, one part, the battery, has taken center stage. With much of the conversation rightfully focused on how to properly recycle batteries, the reality is that the component makes up only around 40 percent of an EV by value, leaving 60 percent — and thousands of other parts — unexamined.
Ecological concerns play a major role in consumers’ desire to purchase EVs, so understanding their vehicle’s impact on the environment has become important. As automakers and stakeholders seek to capture value and drive growth in a world increasingly focused on carbon, there is growing opportunity to incorporate circularity into automotive design and end-of-life disposition.
A framework grounded in reduced waste production and multiple life cycles of raw materials, circularity offers automakers a chance to emerge as first movers while reaping substantial benefits such as increased profitability and reduced supply chain risks.
While numerous barriers to the adoption of a fully circular EV exist — from the complexity of the vehicle to the upfront capital requirements of recycling — there is a strong business case for why the automotive sector should prioritize reusing, refurbishing and recycling vehicle components.
The benefits of implementing circularity into the EV business model include:
- Increased profitability: Circularity is expected to become more profitable in the coming years because of lower recycling costs as volumes scale, lower costs of second-use materials compared with first-use materials and partial isolation from price volatility driven by the scarcity of raw materials.
- Regulatory compliance and political goodwill: Geopolitical risk and regionalism are causing automakers to think more about vertical integration to avoid trading-partner challenges and increasing regulation. With improved circularity, many of these risks can be avoided or mitigated.
- Reduced supply chain risk: Reduced dependency on individual raw material suppliers by using recyclers ultimately results in lower material constraints. Research suggests that deep shortages of some critical metals and rare earth elements mean the world could experience capacity challenges as early as 2024. By creating a system of circular life cycles for vehicle materials, automakers will be much less dependent on raw material inputs from extractive industries.
- Incorporate product enhancements: Advancements in science may result in some materials becoming better and lighter. Having component-level recycling models in place may permit their incorporation into vehicle freshening design cycles and even in-field upgrades to reduce weight or positively improve key performance attributes.
- Enhanced cost-, knowledge-sharing through partnerships: Collaborating with recyclers and reverse-logistics providers can serve as a vital partnership in not only cost-sharing but also knowledge- and information-sharing.
Implementing circular strategies has a unique set of barriers. To achieve the goal of a fully circular car, automakers and Tier 1 suppliers should first obtain the knowledge and skills needed to execute a strategic map and investment case. They can then engage with key stakeholders, including boards, dealers, customers, suppliers and other partners to fully integrate a circular economy into vehicle design.
While the goal should be to have fully recyclable materials incorporated into the vehicle, starting with key components will result in early wins that pave the way toward increased profitability, reduced supply chain risks and other benefits.
Circularity allows for revenue to be generated repeatedly from the same materials through multiple life cycles. As the auto industry continues to head toward completely circular platforms, the question becomes — who will lead the way?