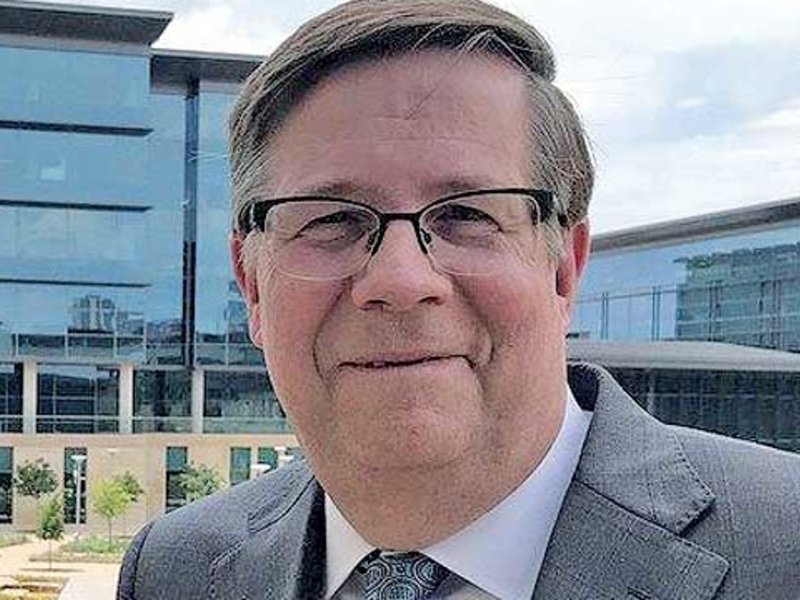
When the U.S. economy last ground to a near halt a dozen years ago and the nation’s auto plants largely stopped producing vehicles, Toyota adopted a bold but expensive strategy that made it stand out from other automakers: It continued to pay all of its workers — even if it didn’t have work for them to do.
Now, as the coronavirus begins to tear through the U.S. auto industry just as the financial crisis did in 2008-09, automakers again must weigh the costs of keeping their employees on the payroll or sending them off to the unemployment line. And even for Toyota, much of that decision may rest on how long they believe the virus will continue to plague their markets.
So far, transplant automakers that have called temporary halts to production operations have each committed to continue to pay their employees while plants remain closed.
Meanwhile, the unionized work force of the Detroit 3 will receive a combination of unemployment benefits and negotiated union subpay while their plants remain idled. Under the 2019 UAW contracts with the Detroit 3, laid-off workers are entitled to unemployment compensation as well as supplemental pay from the union. The UAW tells its members that together, the two will amount to something like 95 percent of non-overtime take-home pay.
The decision by transplant automakers such as Toyota, Volkswagen and Subaru to continue to pay their hourly workers may depend on how long they expect the impact from social distancing and coronavirus to last. While workers at the Asian and European automakers’ U.S. plants may receive more money upfront, UAW workers likely would have more stable incomes if the crisis drags on.
IMG01
During the Great Recession, Toyota Motor North America CEO Jim Lentz said he and fellow executives determined that it would be less expensive long term to keep paying workers than it would to potentially lose them and have to train their replacements when conditions improved.
Speaking to Automotive News a year ago, Lentz said that while the Great Recession initially looked “fairly deep, we didn’t think that it was going to last for a protracted period of time, so it would have been crazy to lay people off, only to bring them back and retrain them.”
Lentz said he and other Toyota leaders used the downtime “to do a lot of training, and once we’ve done all the training we could do, have people work in their communities to keep them on. I think that would always be our first direction.”
The payoff for Toyota was improved quality and “a lot of loyalty,” said Lentz, who is retiring next week. That loyalty paid off in a variety of ways, argues Chris Reynolds, Toyota’s chief administrative officer for manufacturing and corporate resources.
“It brings someone who actually feels like they’re invested in the mission of the plant, and they come up with some amazing ideas that nobody else would come up with,” Reynolds says. “That’s worth a lot. It’s cheaper, but it also drives a lot of value in terms of that team member relationship.”