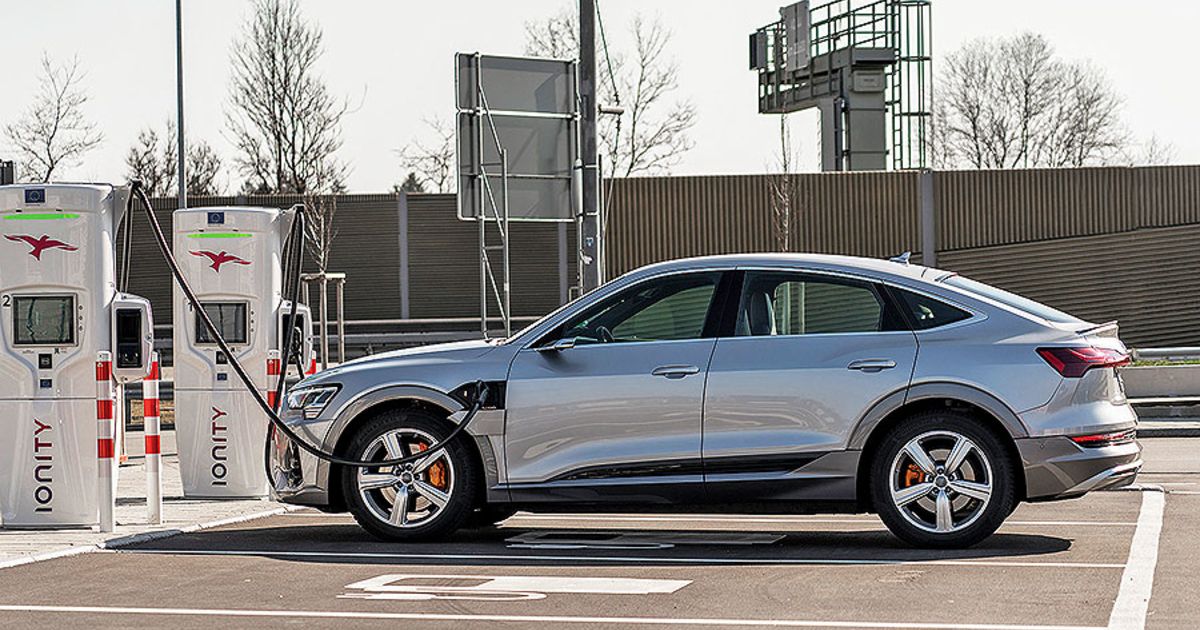
New vehicle components will be left unchanged as the auto industry electrifies — and that applies even to the adhesives that hold those parts together.
DuPont, a global chemical company and one of the auto industry’s largest suppliers, has developed a line of advanced adhesives for electric vehicle batteries it says can help automakers reduce weight, improve safety, allow for more flexible designs and even improve performance and driving range.
The adhesives are in use on a range of EVs and hybrid vehicles, including those made by Audi and Polestar. Christophe van Herreweghe, DuPont global strategy and marketing director, said the company has lined up a “healthy pipeline” of customers for the adhesives as more EVs come to market in the coming years.
“We built up our own knowledge, and when we had requests from the market, we’re able to educate our customers,” he said. “We have, step by step, grown together, and this is why we have materials that are in line with what the customer wants.”
Customer needs can vary from vehicle to vehicle, but EV batteries generally require a different approach to adhesives than parts used in a traditional internal combustion engine vehicle.
DuPont recently published a case study of work it did with a German automaker, which it did not identify, that was looking for ways to reinforce the battery pack on an electric luxury sedan and increase its structural integrity.
The project required the companies to figure out ways to make the battery pack more crash-durable and and to find an adhesive that could work with more than one material at once.
On that project, DuPont created versions of its Betamate and Betaforce bonding adhesives that improved the sedan’s structural integrity while being able to adhere to steel and aluminum.
“It’s not only about making a material and saying, ‘Here you go, have a nice day,’ ” van Herreweghe said. “It’s also making that material work with automakers’ processes.”
On another project, DuPont worked with Audi to develop a bonding material for the E-tron electric crossover that could help boost its driving range and aid with thermal management. DuPont was involved early on as Audi developed the vehicle, van Herreweghe said.
For the E-tron, a new version of the Betaforce adhesive was developed specifically to ensure its battery pack stays at around 77 degrees Fahrenheit and below 140 degrees Fahrenheit when charging.
That thermal management helps the vehicle’s battery system “deliver a range of more than [249 miles] and support super-fast 150kW charging, freeing drivers from ‘range anxiety,’ ” DuPont wrote of the project.
DuPont is now investing in its manufacturing capabilities as automakers roll out dozens of EV models. Last year, the company said it would spend about $30 million to build a facility for adhesives production in China, and it invested $5 million at factories in Germany and Switzerland for automotive adhesives production.
It’s continuing to develop new versions of its existing products.
The company last year introduced its Betaseal 900EI battery pack sealing and bonding adhesive, which DuPont said gives battery packs “reliable environmental sealing and durable bonding” while providing “electrical insulation for sensitive battery components.” It is now in production and “prototyping with multiple global automotive manufacturers,” the company said.
As it develops solutions for the near term, the company is also keeping an eye on emerging battery technologies to ensure that it will have solutions that work with new chemistries and designs, van Herreweghe said.