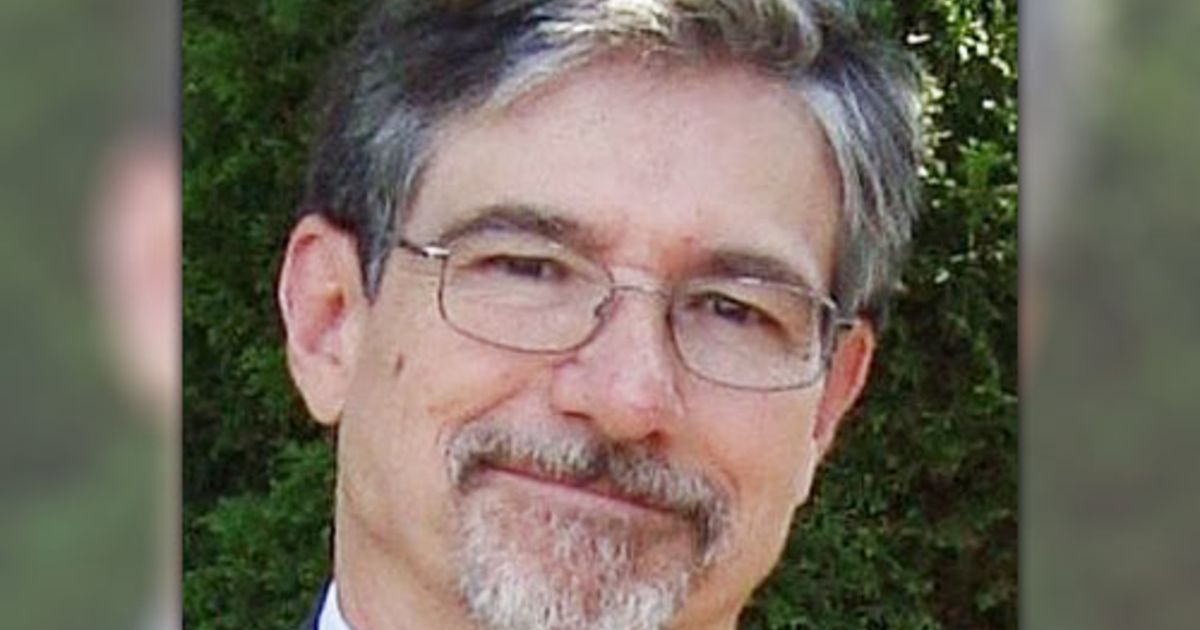
As electric vehicles grow more common, some of us in the driving community will miss the rumble of a finely tuned engine. Among this nostalgic group, some will be EV developers.
That is because the familiar sounds of internal combustion engines and their mechanical subsystems have long masked other, more subtle noises that become easily heard while riding under electric propulsion. Among these are the sound of air rushing past the vehicle exterior, tires rolling on the pavement below and the whir of the HVAC system. Given that EVs have neither engine nor exhaust, these sounds are becoming increasingly irritating for those working to deliver a pleasant cabin noise environment. Their customers have even higher expectations of quietness when operating an EV.
The good news for designers and drivers is that tools exist to mitigate these auditory irritants. Better yet, development teams at automakers are increasingly familiar with them. During the past few decades, vehicle manufacturers have become more comfortable in applying acoustic simulation software to pinpoint potential noisemakers, and they do so long before the design of body panels is finalized and construction of confirmation prototypes is kicked off. This has had a positive effect on sound within the vehicle, allowing noise troubleshooting to concentrate more on manufacturing issues, not to mention significantly reducing hardware prototyping costs and development times.
With acoustic simulation tools, automotive engineers can develop virtual twins of their designs, simulating the many acoustic signatures, then quickly identify and mitigate any over-target noise. Simulations can be repeated until the vehicle design is as quiet as desired.
It wasn’t always like this. Before advanced simulation processes became available, automakers were forced to make educated guesses about the sources of vehicle noise and then proceed with building physical mock-ups to assess their status. In addition to the cost of multiple stages of prototype construction, development teams had to be concerned with the accuracy of their physical mock-ups as designs continually evolved. For instance, a full-scale clay model with a simulated front side glass and truncated cabin space could rapidly become obsolete for assessing wind noise as the size and shape of the glass panel was redesigned.
Such specialized physical mock-ups were also limited in the range of design changes that could be recommended because wind noise can enter the cabin through many paths, such as underbody panels and door seals. This was clearly a cumbersome approach. With decreasing timelines for development, as well as the expanding number of models to be released, evaluating noise fixes via physical models became ever more impractical due to the cost and the time needed to build them.
Wind noise is just one example. There was also the sound of the combustion engine, exhaust and intake, plus noise from the tire contact patches. In the pre-simulation world, each of these required expensive hardware prototypes and often, dedicated laboratory facilities and personnel to attempt noise refinement as best as possible. Extreme stress was experienced near program launch dates by teams whose subsystems were not meeting noise targets. Thankfully, improved acoustic simulation processes have allowed launch pressures to be directed at refining more subtle noise issues.
Enter electric vehicles. Suddenly, the cabin soundscape is filled with very different noises. Overall sound levels from EV powertrains are far lower, though torque ripple and meshing of gear teeth produce audible noise from electric drivetrains, not to mention electronic noises contributed by power inverters. Tire and traffic noise, as well as the sounds of air conditioning and wind buffeting that were once masked by combustion sound, is now loud enough to interfere with occupants’ conversation or enjoyment of the car’s infotainment system. Each of these noisemakers is potentially distracting from the goals of cabin noise quality, raising the bar on vehicle design principles and customer satisfaction alike. Even when the vehicle is parked and charging, battery cooling fans cycling on and off may be annoying to passersby.
Acoustic simulation allows solving many noise problems earlier, which is always better. There is less need for costly physical mock-ups, unnecessary tooling costs or lengthy development cycles. The first confirmation prototype vehicle is now much closer to the right vehicle; one as quiet as it can be while meeting other targets, providing the best possible user experience. So listen up, everyone, as you experience more EV designs. Hear how quiet it can be?